Customers have recently been telling us that General Scanning (now known as Novanta, Inc.) has discontinued the G-series of Galvanometer Optical Scanners. Models in this series include the G102, G108, G112, G115, and G124.
Originally invented in 1975 by General Scanning co-founders Jean Montagu and Pierre Brosens, these scanners have been with us for 45 years!
Customers told us that, at the end of the product’s lifetime, they were paying more than $400 for a single scanner without mirror, mount, controller, or any other accessories.
With these scanners having been designed into a wide variety of equipment, including paint- removal (laser cleaning) systems, dermatology applications and other medical products, customers have scrambled to find a suitable replacement.
We have worked with such customers and helped them to design in the ScannerMAX Compact 506 optical scanner, as a replacement for the venerable G-series optical scanners. The Compact 506 is a scanner that offers superior performance with lower costs, less weight, less power consumption and greater convenience.
Below is a table that summarizes the differences between the General Scanning G-series scanners and the ScannerMAX Compact 506.
Parameter | General Scanning G-series | ScannerMAX Compact 506 |
Servo type | Open-loop | Closed-loop |
Actuator technology | Moving Iron | Moving Magnet |
Scan angle | 4-48 degrees optical, depending on model | Greater than 100 degrees optical |
Weight | 75 grams | 12.8 grams |
Cost | $400.00 (even in high quantities) | $175.00 (quantity 1) |
Current for 10-degrees | 1A (G112); 800mA (G115); 500mA (G124) | 70mA |
Mirror mount | Separate mount is always required | Integrated (separate mount optional) |
Number of wires reqd. | 2 or 4 | 6 or 8 |
G-series scanners were invented 45 years ago. They were open-loop scanners, which means that their accuracy was limited, particularly toward the center of scan, where hysteresis presented a significant hindrance.
On the other hand, the Compact 506 was released in 2012, and it is based on the most modern moving-magnet technology. It is a closed-loop scanner, having an integral analog position sensor that uses optical differentiation techniques. The position sensor offers high stability over time and temperature, and short-term repeatability approaching single-digit microradians.
In the pages below, we review aspects of replacing a G-series scanner with the Compact 506. Due to the smaller size of the Compact 506, it may be possible to directly fit it into the mechanical area formerly occupied by the G-series scanner, thereby slotting it in with no mechanical changes.
SIZE AND WEIGHT COMPARISON
Let’s start with a comparison of the size of the G-series scanners and the Compact 506. Below you will see a picture of a General Scanning G124 on the left, and ScannerMAX Compact 506 on the right. The scanners were placed on notebook paper with lines 1⁄4 inch (6.35 mm) apart.
What is immediately obvious is that the axial dimensions are similar – that is, the dimensions from the top of the scanner (where the output shaft is located) to the bottom of the largest portion of the scanner. Otherwise the Compact 506 is smaller in every other way.
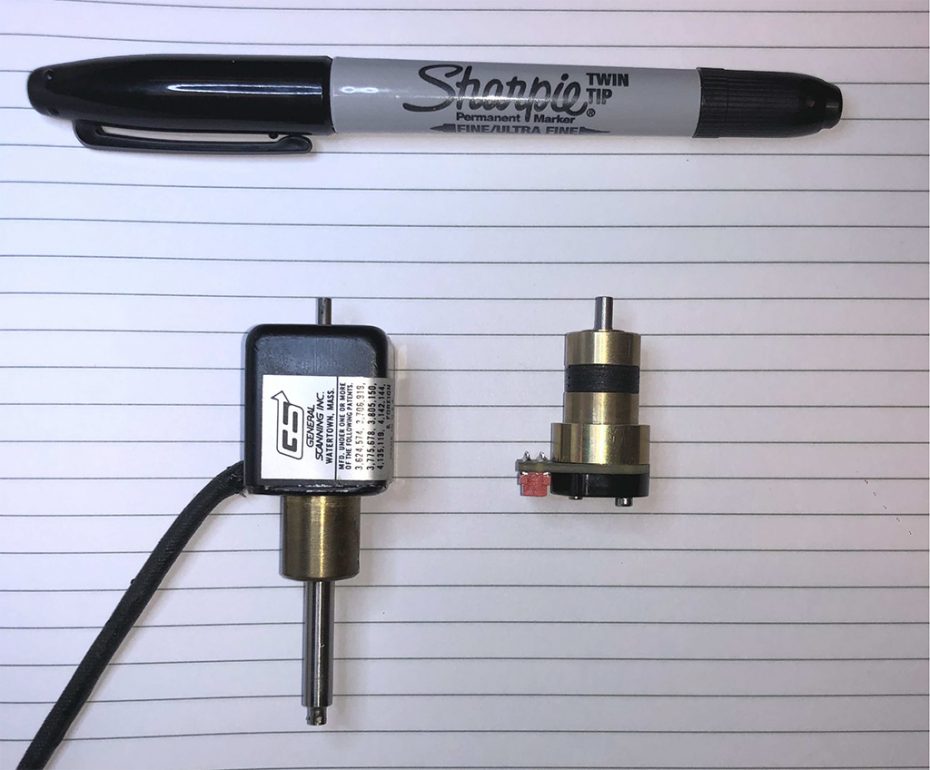
The compact 506 certainly occupies a smaller volume of space, and is lighter too. The General Scanning G-series of scanners is made primarily of iron, brass and copper, and weighs 75 grams. On the other hand, the Compact 506 is made primarily of aircraft aluminum, and weighs a bit more than 12 grams.
MECHANICAL RETROFIT POSSIBILITY
Given that the axial portion of the scanner is similar, and that the other dimensions are no greater, and given that the cylindrical brass area of the G124 is what is commonly used for mounting, it means that the “back cap” of a Compact 506 could be replaced with a plug-style back-cap. When this is done, the same cylindrical mounting portion remains, and thus the Compact 506 could be slotted into exactly the same physical area and mount formerly used by the G-series scanners. This is shown in the picture below, where we 3D-printed a plug-style back cap just as an example of what could be done.
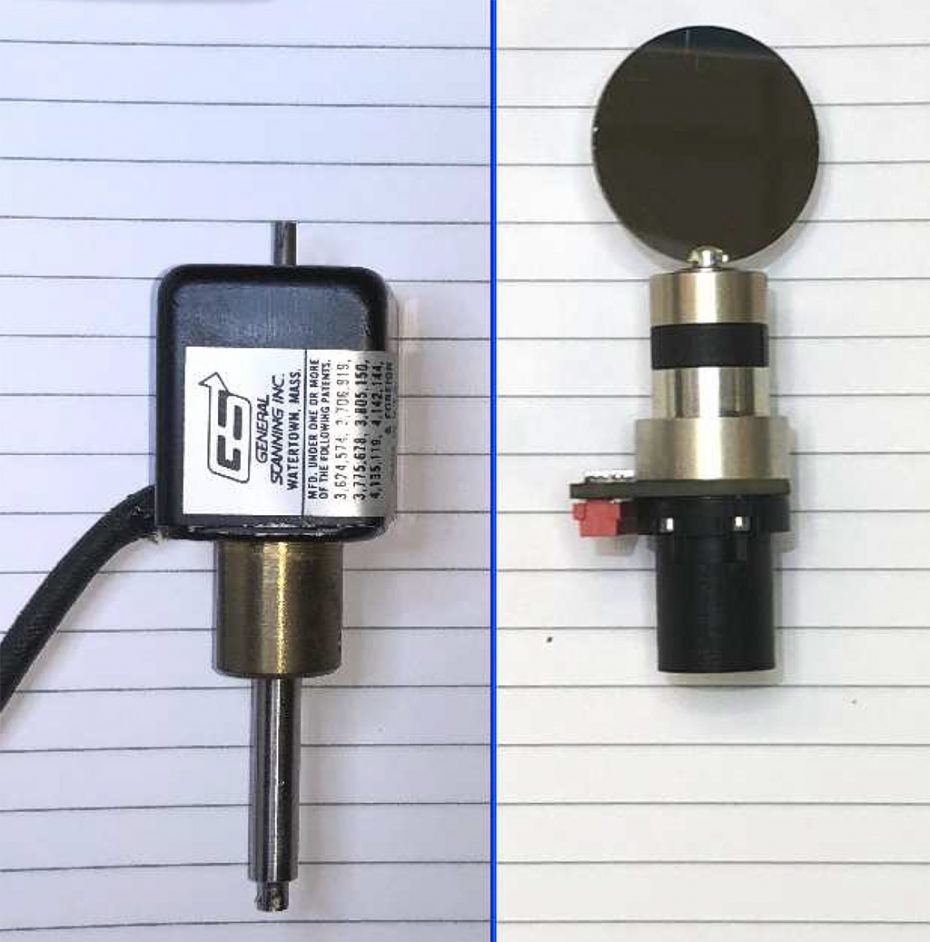
ELECTRICAL / WIRING CHANGES NEEDED
Due to the fact that the General Scanning G-series was open-loop and thus, did not have a position sensor, the drive circuitry was relatively simple. Moreover, in many cases, customers could drive the scanner with a cable having only 2 wires – wires that drive the coil. Admittedly, this provided a certain level of convenience. However, the cost of this convenience was relatively high electrical power consumption. For example, the datasheet lists “sensitivity” for the model G-115, at 80mA per degree. This means if you want the scanner to hold and maintain a 10-degree position, it required the servo driver and wiring to carry 800mA, heating the scanner.
On the other hand, the Compact 506 is a closed-loop scanner. Because of this, the actuator was designed to require relatively little current to hold a particular position. To hold a 10-degree position requires only 70mA of electrical current. This will not cause heating of the scanner.
The Compact 506 position sensor uses a differential analog optical technique. Two pairs of photodiodes are used to ensure stability and sensitivity to rotary motion, while being insensitive to radial motion that might be caused by imbalanced loads. The photodiodes and LED illuminator will require four wires to operate. However, current for the LED is typically on the order of 10mA, and current from the photodiodes is well under 1mA, so small wires can be used for all of these signals. The actuator coil requires an additional two wires, for a total of 6 wires needed. Applications requiring higher performance or better noise immunity may benefit from an additional two wires as ground/shield wires, for a total of 8. Note that if the distance between the servo driver and the scanners is small, simple ribbon cable may be used to connect the two.
ADDITIONAL BENEFITS OF CLOSED-LOOP
Since the Compact 506 is a closed-loop scanner, a precise analog position signal is always available, as well as other signals including position error, velocity and coil current. Any of these or all of these may be used as feedback for safety systems or performance confirmation signals within an overall system, thus adding to the robustness of products that use this scanner.
INTEGRATED MIRROR MOUNT
Unlike the G-series scanners, which have a 2.4mm solid shaft, requiring a separate mount for a mirror, the Compact 506 has a 3mm slotted shaft with integrated mirror-back-support. The mirror can be directly glued into the shaft, easing system integration and reducing cost.
OEM SERVO DRIVER SCHEMATIC OFFERED FOR FREE
We offer customers the schematic of a suitable servo driver that can be used with the Compact 506 at no cost. This servo driver can thus be integrated directly into customer’s electronics. The servo driver electronics typically involves a small number of op-amps per axis, plus a power amplifier IC.
The servo driver can run off of a single +12V supply, or it may operate from +/-12V, +/-15V or +/-24V, depending on scanning performance requirements as well as the customer’s existing power availability. Using double-sided surface mount components, a two-axis servo driver can be fashioned in as little board space as a few postage stamps. This is usually smaller than the driver circuitry used for G-series open-loop scanners.
OFF-THE-SHELF KITS AVAILABLE TO QUICKLY GET STARTED
There are several servo driver options available off-the-shelf for immediate purchase. For prototyping and system evaluation, the best option is our Mach-DSP, fully digital servo driver. This includes a companion program that runs on the PC and connects to the servo driver via USB cable. This PC program offers tools such as function generator, oscilloscope, and dynamic signal analyzer. Five separate servo control laws can be evaluated, and different power supply scenarios can be simulated, allowing you to fully evaluate the ultimate requirements for a servo driver and power supply. The Mach-DSP can be connected to the scanners via cable lengths ranging from 10-inches to 5 meters, all of which we have in stock. A complete system is pictured below.
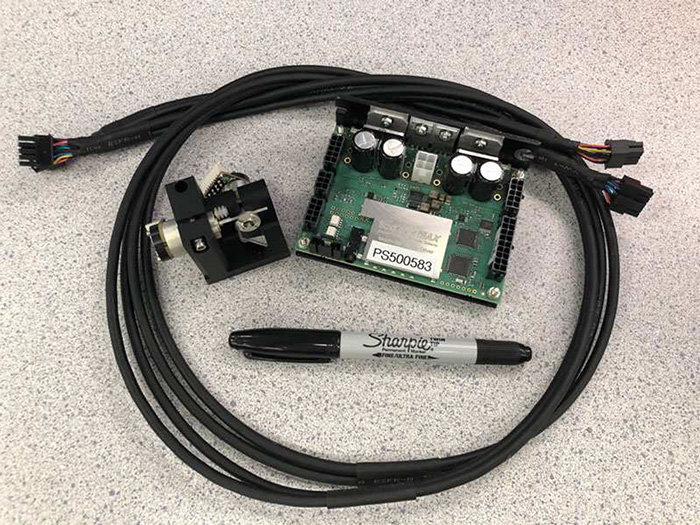
Below is a picture of the built-in Oscilloscope. Nearly 100 test points are available to measure everything from position, to velocity, to current, and heat.
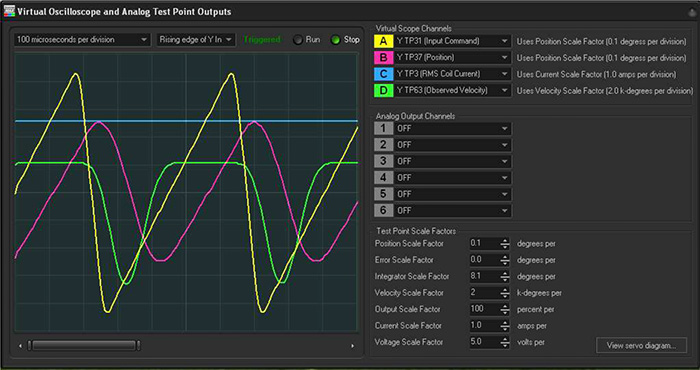
CREDIT-CARD-SIZED SERVO ALTERNATIVE
Depending on power availability and performance requirements, another option is a two-axis servo driver that is the size of a credit card and runs off of +12V. The entire two-axis system is shown below.
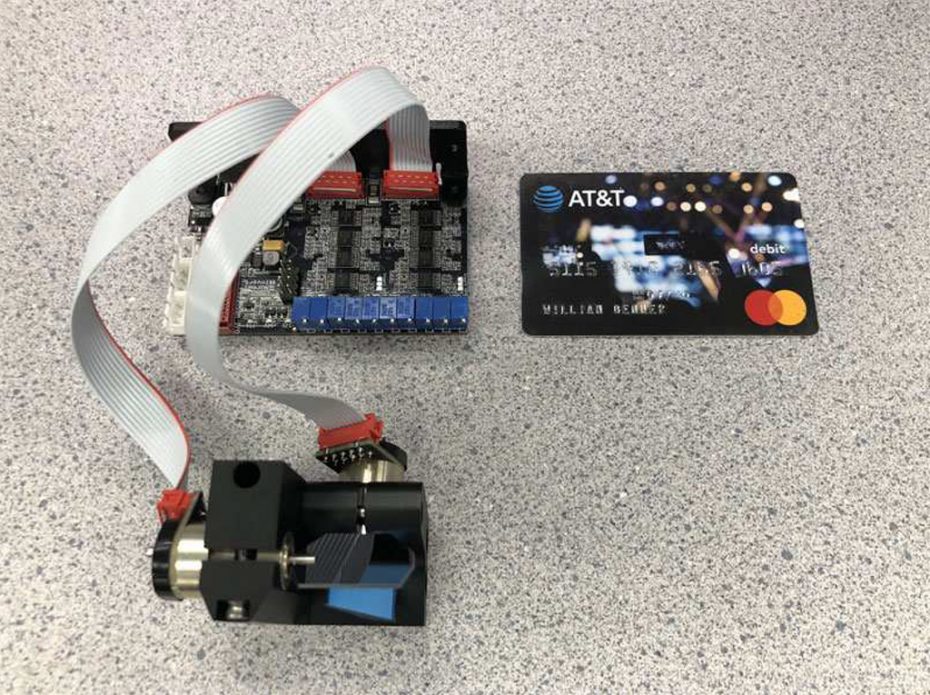
PATENTED, AWARD-WINNING TECHNOLOGY
The Compact 506 is covered by 11 US and International patents. It won the First Place Fenning Award for Technical Achievement in 2014.
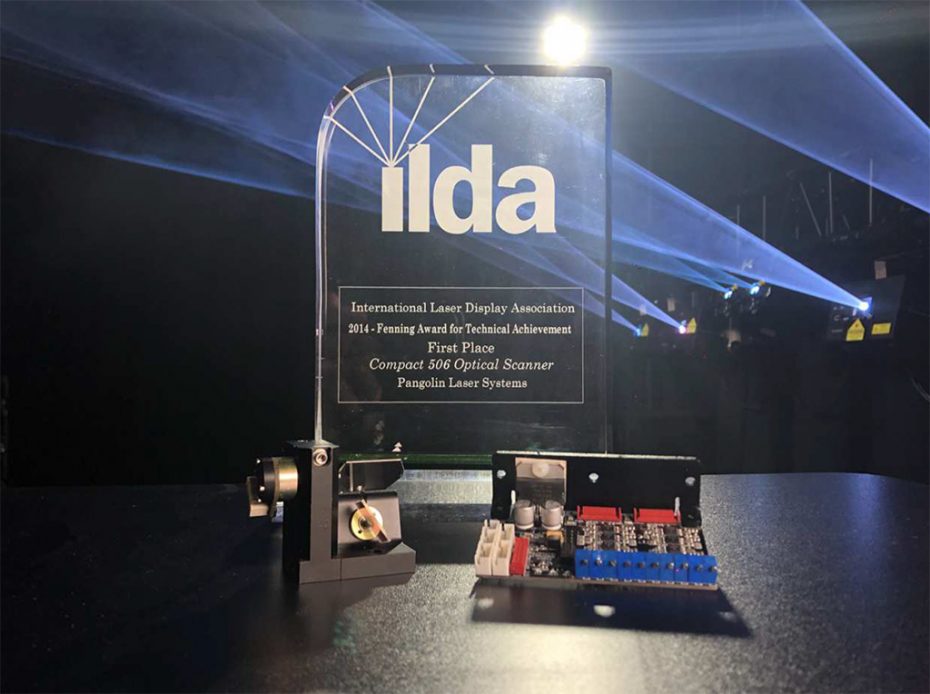
Download the press release below:
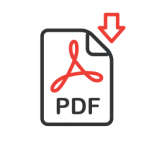